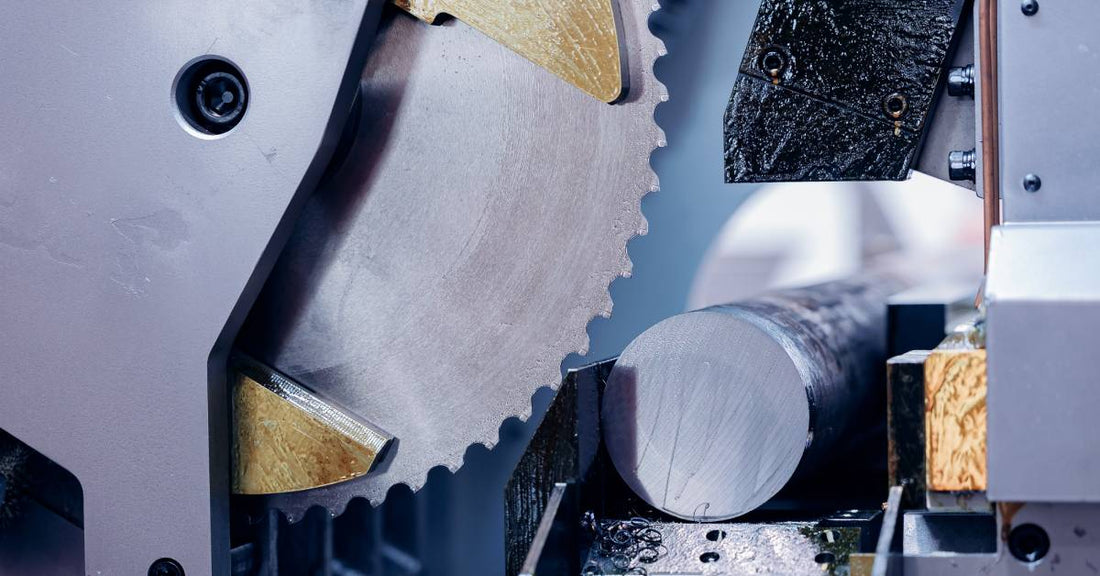
Strategies for Avoiding Burr Formation in Metal Cutting
Burrs are unwanted raised edges, sharp projections, or material residues left on a workpiece during cutting, drilling, milling, or other machining processes. These imperfections occur due to the deformation of the material as the cutting tool removes parts of the workpiece.
Burrs reduce the aesthetic quality of the finished product. They also can impair the functionality of a component as sharp edges may hinder proper assembly, interfere with moving parts, or create safety hazards for users. Additionally, burrs may act as stress concentrators, leading to cracks over time. Cracks can compromise the structural integrity of the material, particularly in applications requiring precise tolerances or stress resistance.
In industries where efficiency is critical, such as aerospace, automotive, and medical device manufacturing, minimizing or eliminating burr formation is essential to maintain quality and keep production streamlined.
Minimize imperfections with these strategies for avoiding burr formation in metal cutting. Use the proper tools and techniques to maintain the highest standards in your work and achieve flawless results.
Understand Why Burrs Form
Before tackling the problem of burr formation, it’s essential to understand why it happens. Burrs typically form during the metal-cutting process as a result of material deformation. This phenomenon occurs when the force applied during cutting causes stress along the cutting path. If the cutting force exceeds the material’s ability to withstand it, or if the material is not adequately supported, the edges of the metal may bend, resulting in unwanted burrs.
Several factors contribute to this issue. For example, when the cutting force is too high, the material may deform more significantly, making burr formation almost inevitable. On the other hand, if the metal lacks proper support during the cutting process, the structural integrity of the edges weakens, increasing the likelihood of burrs.
Additionally, improper maintenance of cutting tools often plays a crucial role. Dull tools may fail to create clean, precise cuts and instead tear or compress the material, leading to burrs.
Choose the Right Equipment

No matter how skilled you are, your tools are a direct extension of your precision. Selecting the best equipment plays a pivotal role in achieving burr-free cuts.
Cold Saws
Cold saws are widely regarded in the industry for their ability to deliver clean, precise cuts with high accuracy. One of their key advantages is their ability to reduce heat during operation, which minimizes material deformation and burr formation. This quality makes them ideal for applications that require smooth edge finishes.
Band Saws
Band saws are highly reliable for cutting a wide range of materials, from metals and plastics to wood, providing flexibility and consistent performance across various tasks. They are especially useful for projects that require straight or curved cuts in thicker materials, ensuring uniform results even with challenging materials.
Last Cutters
Laser cutters excel at creating intricate designs and detailed finishes. Their high level of precision and ability to handle complex shapes make them perfect for cutting metals, plastics, and other materials where accuracy and smooth edges are essential. Laser cutters are valuable in industries like manufacturing, aerospace, and product design, where fine detailing and a flawless finish are often top priorities.
Selecting the right cutting tools for your needs ensures precision, efficiency, and a professional standard of work in every project.
Use Sharpened Blades
Blunt tools are the enemy of clean, precise cuts in metalworking. Dull cutting blades increase friction, requiring more force to complete the cut, which leads to uneven pressure and irregular material deformation. This, in turn, results in burr formation, which can compromise the quality of the finished product and create additional work during post-processing. Regularly sharpening your blades ensures your tools perform at peak efficiency, delivering accurate, consistent, and smooth cuts every time.
Signs of blade dullness often include rough finishes on your cuts, jagged edges, or an unexpected increase in the effort needed to operate the tool. Even a minor imperfection in the blade’s edge can significantly impact its performance and the quality of your work. If these issues arise, it is crucial to resharpen the blade promptly and assess whether a replacement might be more effective.
Optimize Speed and Feed Rate
One of the best strategies for avoiding burr formation in metal cutting lies in fine-tuning your operational parameters, particularly speed and feed rate. These factors directly influence heat generation, cutting forces, and material deformation during the process, all of which contribute to burr creation.
Running your equipment too fast increases friction and heat, leading to material softening and potential deformation as the metal becomes less stable under high temperatures. This can result in jagged or excessive burrs on the edges of the cut.
Conversely, operating at too slow a speed or using an imbalanced feed rate can hinder the smooth cutting action needed to minimize burrs. Slow speeds may fail to efficiently shear the material, resulting in uneven edges or incomplete cuts.

Use Proper Cutting Technique
Skilled handling of cutting equipment and attention to detail directly impact the quality of your cuts. By carefully adjusting angles and depth, you can minimize imperfections, such as burrs, and ensure a smoother finish.
Angles
Cutting at an incorrect angle can lead to uneven pressure across the material, which often deforms the edges and results in unwanted burrs. A consistent and accurate cutting angle ensures uniform material removal, reduces the risk of edge deformation, and minimizes the need for post-cut cleanup. Always refer to your tool’s specifications, and adjust accordingly to avoid unnecessary errors.
Depth
Too shallow or too deep a cut can significantly compromise your work. Shallow cuts fail to slice cleanly through the material, while overly deep cuts place unnecessary stress on the blade and the workpiece, often leading to burrs.
Maintaining a consistent, appropriate depth throughout the cutting process ensures that the material glides evenly under the blade. This uniformity preserves the structural integrity of the material and produces clean, professional edges with minimal rework.
Set Yourself Up for Success With the Right Metal Cutting Tools
Each of these strategies contributes to a cleaner, more efficient process, ensuring every cut meets high professional standards. But quality results demand quality tools. If you’re ready to tackle burr formation head-on, invest in the best cutting blades for the job.
Here at Cold Saw Shop, we can help you find the perfect aluminum cutting blade for a circular saw, along with many other options. Choose the right tools, and enjoy the burr-free results.