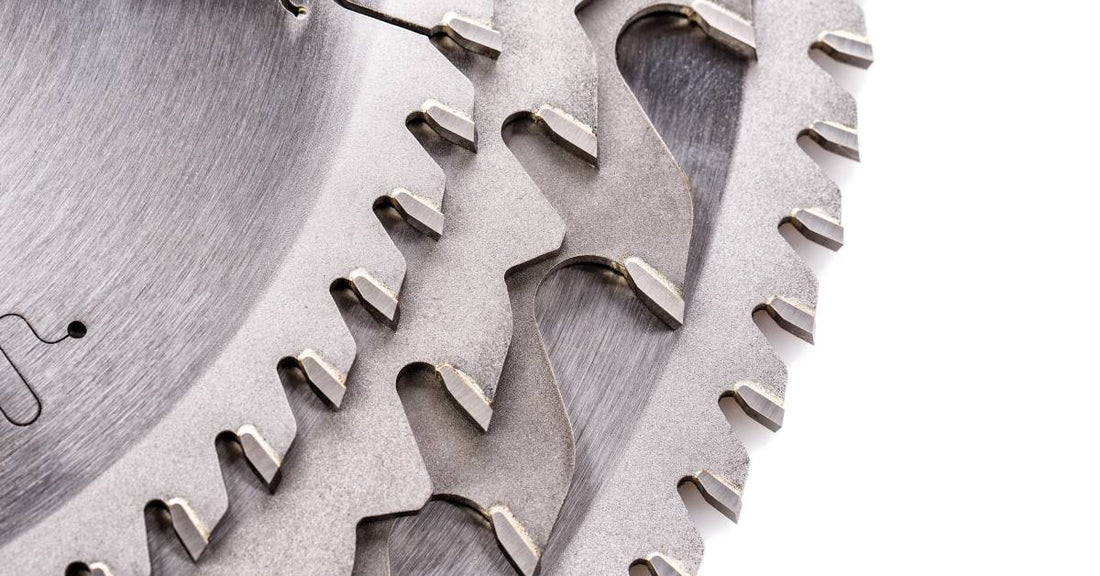
Saw Blade Tooth Count: How To Choose the Right Saw Blade
Your choice of sawblade can make a huge difference when you’re working with precise metalworking. The tooth count of a saw blade is a critical factor that determines both the quality of the cut and the efficiency with which a job is completed. Today, we’re looking at saw blade tooth count and how to choose the right saw blade based on this information.
Understanding Saw Blade Tooth Configuration
The configuration of saw blade teeth significantly impacts the performance and suitability of the blade for specific metalworking tasks. Tooth configuration encompasses several aspects, including the tooth shape, gullet size, and tooth angle. Each of these components works in concert to influence the cutting action, chip removal, and overall finish quality of the cut.
A positive tooth angle is more aggressive and facilitates faster cuts, which is ideal for thicker materials. On the other hand, a neutral or negative tooth angle provides more control and is better suited for thinner materials or fine finish work. Gullet size (the space between teeth) also plays a pivotal role in chip evacuation, preventing clogging and overheating, which can lead to blade damage. Understanding these configurations allows metalworkers to make informed decisions when selecting a saw blade tailored to their specific needs, ensuring efficiency and precision in their cutting operations.
Tooth Count and Metal Thickness
The relationship between tooth count and metal thickness is crucial in achieving optimal cutting performance. A saw blade with a higher tooth count is usually a better option for cutting thinner metals. This is because more teeth per inch (TPI) results in smaller, finer cuts that require less force and generate less vibration, yielding a smoother finish. For example, a blade with 18 TPI is suited for thin-gauge materials like sheet metal or thin-walled tubing, ensuring clean edges without causing material distortion.
Cutting thicker metals necessitates a blade with a lower tooth count. Fewer teeth per inch means each tooth can remove more material with each pass, which is essential for maintaining efficiency and preventing the blade from binding or overheating.
A blade with 10 TPI might be used for thicker metal sections, such as beams or heavy tubing, allowing for quicker, more aggressive material removal. Selecting the appropriate tooth count based on the thickness of the metal you’re cutting not only enhances cutting performance but also prolongs the life of the saw blade, reducing the need for frequent replacements due to wear or damage.

The Role of Tooth Geometry
Tooth geometry plays a fundamental role in determining the effectiveness of a saw blade for specific metalworking applications. The geometry of a saw blade's teeth encompasses various elements such as the bevel, pitch, and tooth shape. These elements work meticulously to optimize cutting performance based on the type of material and the desired finish quality.
A saw blade with beveled teeth can create a shearing action that is especially beneficial when cutting harder metals, as it reduces the cutting force required and minimizes burr formation. The pitch, or the distance between the teeth, also significantly influences how the blade interacts with the material.
A smaller pitch ensures that more teeth are engaged in the cutting process at any given time, which is ideal for creating smooth, precise cuts in thin materials. Alternatively, a larger pitch is more effective for cutting thicker materials, allowing for more substantial material removal with each tooth pass.
The overall shape of the teeth, whether they are flat-topped, hooked, or alternating, can greatly affect the cutting dynamics. Flat-topped teeth provide uniform cutting pressure and are suitable for straight cuts, while hooked teeth offer more aggressive cutting capabilities, making them ideal for faster, rougher cuts. Alternating tooth shapes, where teeth switch between left-leaning and right-leaning, can help to balance the cutting force and reduce the risk of blade drift.
Material Compatibility
When trying to figure out how to choose the right saw blade, you want to consider the material on the tip of the teeth as well as the number of teeth and the spacing between them. Choosing a saw blade with the correct material compatibility is crucial for achieving the best results in metalworking projects. Different metals have unique properties that necessitate specific types of saw blades to ensure clean, efficient cuts without damaging the material or the blade.
Ferrous metals such as steel and iron generally require saw blades with hardened teeth and specific coatings that can withstand the higher temperatures generated during the cutting process. These blades rely on high-speed steel (HSS) or carbide-tipped materials, providing the necessary durability and heat resistance.
On the other hand, nonferrous metals like aluminum, copper, and brass are softer and more malleable and can quickly clog up traditional saw blades, impairing cutting efficiency and causing overheating. Blades designed for nonferrous metals usually feature larger gullets to facilitate better chip evacuation and often have a higher tooth count to ensure smooth, clean cuts without material deformation.
By selecting saw blades that are ideal for the material at hand, metalworkers can optimize their cutting processes, reduce blade wear, and achieve superior finish quality. Understanding material compatibility helps ensure that you execute each cut with maximum efficiency and minimal risk of blade damage or subpar results.

Cold Saw Blade Advancements
Recent advancements in cold saw blade technology have significantly enhanced the metal cutting process, offering improved efficiency, precision, and durability. Many modern cold saw blades use advanced materials such as high-speed steel (HSS) and tungsten carbide, which provide exceptional hardness and heat resistance.
These materials ensure that the blades maintain their sharpness longer, even under intensive use, reducing the need for frequent replacements. Innovations in tooth geometry, such as unique bevel angles and optimized pitches, have also contributed to superior cutting performance, allowing for smoother, cleaner cuts with reduced burr formation.
Advances in coatings, such as titanium nitride (TiN) and zirconium nitride (ZrN), work to increase the blades’ life span by minimizing friction and enhancing heat dissipation. These coatings help prevent material buildup on the blade, ensuring consistent cutting quality and reducing downtime for blade maintenance.
Ready to elevate your metalworking projects with superior cutting performance? Whether you're cutting steel or iron or need a specialized aluminum cutting blade for circular saws, we have the perfect solutions to meet your needs. To learn more about the blades we offer for your specific metalworking needs, Contact Cold Saw Shop today, and a member of our team will be happy to assist you.