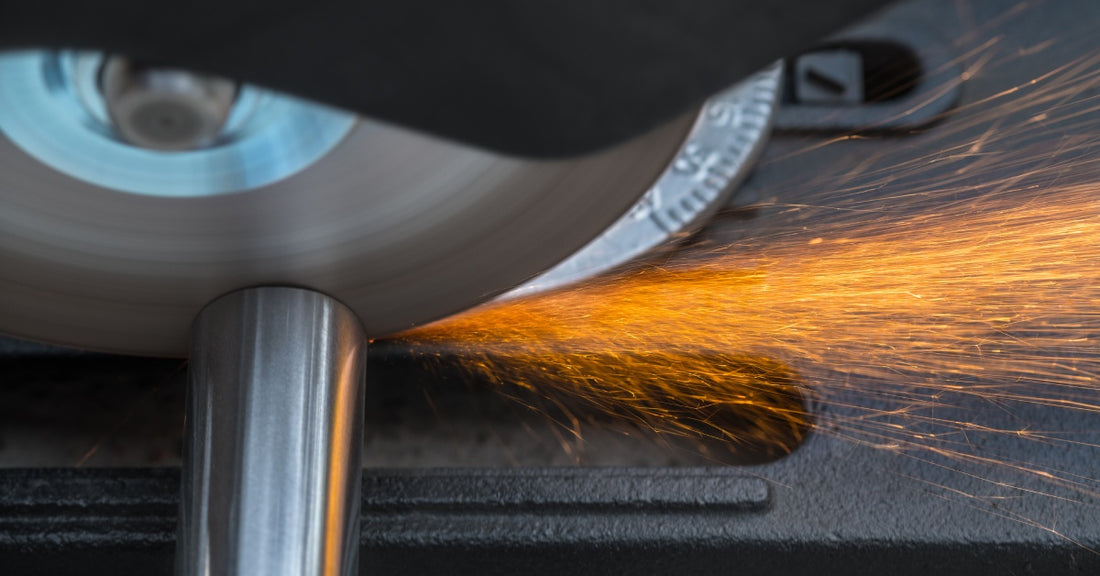
Factors To Consider When Choosing a Cold Saw Blade
Choosing the right cold saw blade is crucial when you’re cutting metal. Different metals have different degrees of toughness or coarseness, and blades themselves have even more details to bear in mind.
Cold Saw Shop is always here to help, and we want to go over a few factors to consider when choosing a cold saw blade. You may find even the toughest metalworking projects go a lot more smoothly when you have the right blade. On top of that, using a suitable blade can also help ensure that you get better performance and longevity out of your tools.
Blade Material
Saw blades come in many different materials, and these can play a major factor in its performance and durability. Some of the most common options for cold saw blades are high-speed steel (HSS) or carbide-tipped materials.
High-speed steel blades are very tough and can withstand high temperatures, making them suitable for cutting through tough metals, such as steel and iron. Carbide-tipped blades are a combination of carbide and steel, which offers enhanced cutting precision and fantastic blade longevity. Carbide-tipped blades are good for cutting non-ferrous metals and are much less prone to wear and tear over time.
Selecting the appropriate material for your blade depends on the specific type of metal you intend to cut and your project’s demands.
Tooth Geometry
Tooth geometry plays an essential role in the efficiency and quality of the cuts a cold saw blade produces. The shape, angle, and spacing of the teeth influence critical factors, such as cutting speed, feed rate, and the finish of the cut. Some of the most common shapes of cold saw blade teeth are flat, trapezoidal, or even alternating shapes.
Manufacturers tailor these distinct profiles to best suit different applications and materials. The angle of the teeth, known as the hook angle, determines the aggressiveness of the cut. A positive hook angle is ideal for cutting softer metals with ease, while a negative hook angle provides better control and precision for harder materials.
Additionally, tooth spacing, or pitch, can impact the smoothness of the cut. Finer pitches work better for thin or delicate materials, whereas a coarser pitch is more effective on thicker and more robust metals. Understanding these aspects of tooth geometry ensures that you select a blade that meets the specific requirements of your metalworking project, optimizing both performance and blade longevity.

Blade Coating
When considering factors for choosing a cold saw blade, many people think about material but may neglect the coating. Different coatings can provide a range of benefits, including increased durability, reduced friction, and improved heat resistance. Even with a traditional aluminum cutting saw blade, the right coating can enhance performance and make it a suitable option for tougher jobs.
For instance, a titanium nitride (TiN) coating has exceptional hardness and can help extend a blade’s life when it’s cutting through harder metals. This coating also offers excellent resistance to wear and oxidation, making it ideal for high-speed applications.
Another popular option is chromium nitride (CrN) coating, which provides a strong protective layer that reduces friction and prevents material buildup on the blade, ensuring cleaner cuts and minimizing downtime for maintenance.
Some folks may invest in a blade with diamond-like carbon (DLC) coatings, which are some of the hardest options and greatly reduce friction, making them suitable for cutting abrasive materials. Choosing the right coating for your cold saw blade depends on the specific requirements of your cutting tasks and the types of materials you work with.
By selecting a blade with the appropriate coating, you can achieve better cutting efficiency, reduced wear, and longer blade life. This will ultimately enhance the overall productivity of your metalworking projects.
Blade Diameter
Blade diameter refers to the overall size of the saw blade from edge to edge, and it determines the maximum depth and width of the cut you can achieve. Cold saw blades come in various diameters, typically ranging from 8 inches to over 20 inches, allowing users to select the appropriate size for their specific applications.
A larger blade diameter can handle thicker materials, making it suitable for industrial applications where you need to rely on heavy-duty cutting. Larger blades can also offer longer, more continuous cuts, which reduces the need for blade changes. However, smaller blade diameters serve a distinct purpose and are ideal for precision work and cutting through thinner materials.
When selecting the blade diameter, you want to consider your saw’s capabilities and limitations. You should also take the time to make sure that the saw’s specifications match the diameter of the blade you intend to use. This is because using an incompatible size can lead to operational issues or even damage to the machine.

Compatibility With Your Saw Machine
Ensuring compatibility between your cold saw blade and saw machine is crucial for achieving optimal performance and safety in your metalworking projects. Each saw machine has specific requirements and limitations regarding the type and size of blades it can accommodate.
As a result, you must verify that the blade you choose matches the machine's specifications. Key factors to consider include the arbor size, RPM (revolutions per minute) rating, and the maximum and minimum blade diameters.
You should also pay attention to the arbor size, which refers to the hole in the center of the blade that fits onto your saw’s spindle. Even if the diameter and size of the blade are perfect, they won’t do you much good if your arbor is too big and causes wobbling or instability during cutting operations.
Using a blade with the correct RPM rating is equally vital, as a mismatch can lead to inefficient cutting, excessive wear on the blade, or potential damage to the machine. Additionally, ensuring that the blade diameter falls within the machine's specified range is essential to maintain safe operation and achieve precise cuts.
By considering all these factors, you can make an informed decision and make sure that you have a saw blade that’s suitable for the job and compatible with your specific equipment. The right blade not only enhances your cutting efficiency but also contributes to the overall quality and precision of your work. Whether you're cutting steel, aluminum, or other metals, selecting the appropriate blade is key to achieving excellent results.
No matter what type of blade you need, you can find it here at Cold Saw Shop. We have blades of different materials, coating options, sizes, and styles to help tackle your hardest jobs. Whether you need HSS blades for tougher metals or carbide-tipped blades for high-volume production, we have you covered.