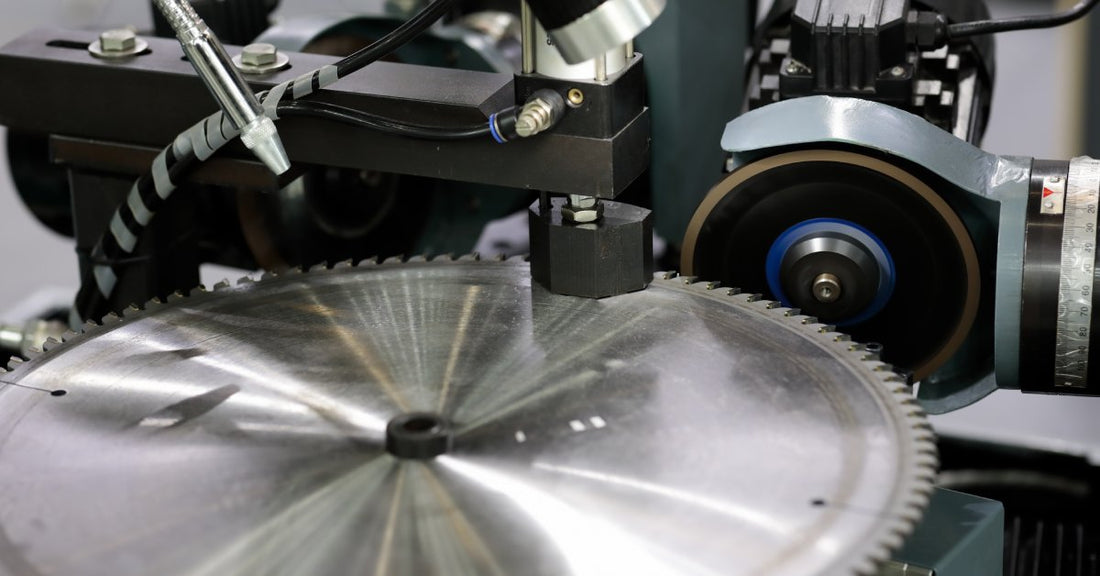
15 Issues To Watch for With Carbide-Tipped Saw Blades
Carbide-tipped saw blades offer durability and precision across various cutting applications. Yet even the best tools can present challenges when they’re not maintained or used correctly.
There are certain issues to watch for with carbide-tipped saw blades that could affect their performance and lifespan. Understanding these common problems is the first step to ensuring optimal results and protecting your investment.
1. Damaged Teeth
A damaged tooth is one of the quickest ways to compromise your blade’s performance. It can occur when the blade strikes a hard object, such as a nail or dense knot in the material you’re cutting. You’ll notice uneven cuts or vibrations during operation.
To prevent this, inspect your material for hidden obstructions, and handle the blade carefully to avoid accidental damage during handling or storage. If damage occurs, it’s best to replace or repair the blade promptly.
2. Uneven Tooth Spacing
Carbide-tipped blades have precise tooth spacing for specific materials. If a manufacturer has deviated from the proper design specifications, the blade may struggle to cut efficiently. This issue often results in overheating or jagged cuts.
To avoid this, select a blade that matches your application perfectly, such as a quality saw blade for cutting aluminum. Choose reputable brands that adhere to quality manufacturing standards.
3. An Unsecure Blade
If the blade isn’t properly fastened to the saw, you might notice wobbling during operation or erratic cutting patterns. This often happens if the blade is not tightened correctly during installation or if there’s wear in the mechanism holding the blade in place. Always ensure you’ve fastened the blade securely before using the machine, and periodically check for any loosening that may occur over time.
4. Improper Clamping
Clamping plays a pivotal role in ensuring clean, precise cuts. Without proper clamping, the material may shift during the cutting process, resulting in inaccurate results or leaving teeth damaged. Always double-check that your clamps are holding the material securely, and distribute pressure evenly to maintain stability.
5. A Rusting Blade
Another one of the big issues to watch for with carbide-tipped blades is rust. It compromises the blade’s sharpness and durability, leading to decreased cutting efficiency.
Moisture and improper storage are the most common causes of corrosion. Always store your blades in a dry, temperature-controlled environment, and consider using protective coatings or rust inhibitors to preserve their surface integrity.
6. A Dulling Blade

Despite their toughness, carbide teeth can dull over time with regular use. A dull blade requires more effort to cut and results in uneven or torn edges. Composite materials or abrasive surfaces accelerate this wear.
Maintaining a sharp blade is crucial, and Cold Saw Shop offers professional blade sharpening services to keep your tools performing at their best. If you notice a drop in performance, bring your saw blades to us, and consider replacing them when needed.
7. Misaligned Speed and Feed Rate
Your saw’s speed and feed rate must align with both the blade’s capabilities and the material you’re cutting to ensure efficient performance. Mismatched settings can strain the blade, leading to overheating, deflection, or premature wear. Always consult the blade’s specifications, the material requirements, and manufacturer recommendations to properly configure your machine before making cuts.
8. Torsional Vibration
When a blade twists or bends along its length during operation, it leads to torsional vibrations. Over time, these vibrations can weaken the blade and compromise the precision of your cuts. Common causes include excessive cutting speeds, improper material clamping, or using a worn blade. To fix this, reduce your cutting speeds, ensure the material is securely clamped, and replace any blades showing signs of torsion-related wear.
9. Lateral Vibration
Lateral vibration pertains to the side-to-side movement of the blade during operation. This can cause uneven cuts, excessive noise, and damage to your carbide tips. It can result from an improperly balanced blade or a loose mounting structure. Make sure to balance your blade regularly and ensure it is fully tightened and securely attached to the saw.
10. Resonance
When vibrations from the saw machine amplify those in the blade, excessive movement and instability during cuts can occur. This often happens when incorrect settings enhance natural frequencies. Signs include wavering cuts, increased noise, and reduced precision.
To minimize resonance, use dampening systems or adjust the saw’s speed to avoid problematic frequencies.
11. Overloaded Machine
Overloading happens when you force the machine to cut through material that exceeds its capacity or when the blade is worn and less effective. This not only stresses the saw blade but can also damage the machine itself.
Signs of overload include resistance during cuts and overheated blades or motors. Prevent this by ensuring the blade and machine match the material specifications and replacing worn components promptly.
12. Resistance While Cutting
If you notice excessive resistance or the need to apply extra pressure during cutting, it’s often due to a dull blade or misaligned teeth. Continuously forcing the material through a resistant blade can lead to dangerous overheating and uneven cuts. Mitigate this by sharpening your blade once resistance becomes evident, and ensure proper material alignment before cutting.
13. Jagged Cuts
Unclean cuts typically result from dull blades, poor blade quality, or improper feed rates. If your cuts become uneven or riddled with rough edges, check your blade for dullness, ensure the speed aligns with your material, and verify that your blade is suitable for the application.
14. Clogging
Over time, debris such as dust, material fragments, and small particles from previous cuts can accumulate between the teeth of the blades. This buildup reduces performance and precision, making cutting less efficient and potentially causing the blade to wear out faster or sustain damage. Clogging can also lead to uneven cuts and increased strain on your equipment.
To prevent this, make it a habit to clean your blades thoroughly after each use, using appropriate tools or cleaning solutions designed for your specific blade type. Regular maintenance will help your blades last longer and ensure optimal performance.
15. Poor Saw Blade Manufacturing
Low-quality materials, inconsistent tooth spacing, and inadequate bonding of carbide tips reduce longevity and performance. Inferior blades frequently bend, dull quickly, or fail to meet cutting expectations.
To avoid this entirely, invest in high-quality carbide-tipped blades from trusted suppliers. Cold Saw Shop has the blades you need to ensure precise, reliable cuts every time. You can avoid most of the issues on this list by using well-made blades for all of your projects.