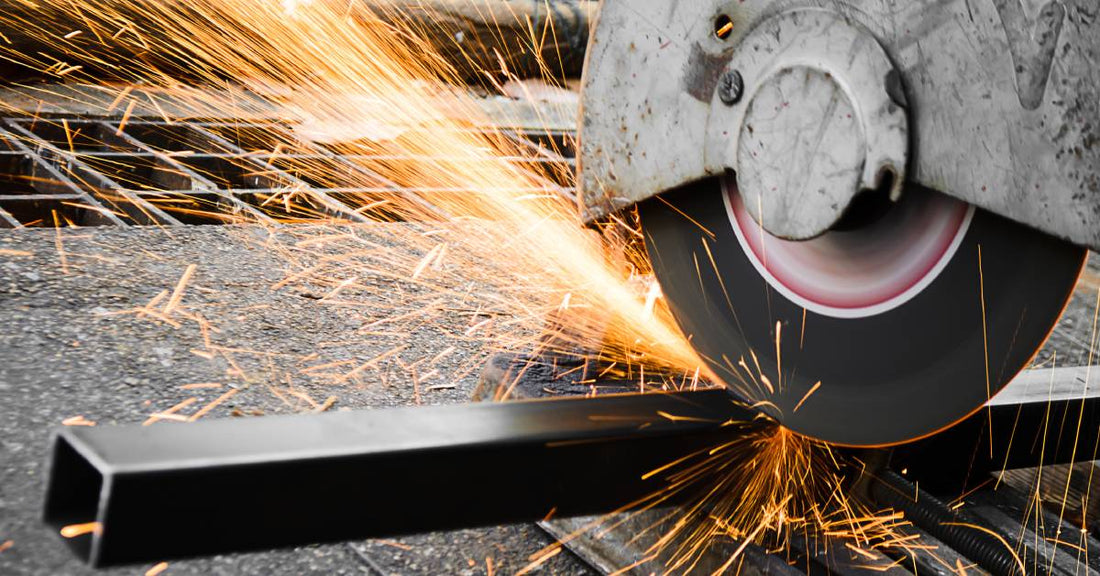
Understanding Cutting Speed and Feed Rate for Metal Cutting
Metalworking is more than simply cutting into a piece of steel or aluminum. It’s a precise science, driven by exact calculations and the right tools. If you’re new to the industry, you’ve likely already encountered terms like “cutting speed” and “feed rate. ” These concepts can feel overwhelming at first.
But, understanding cutting speed and feed rate for metal cutting is vital to achieving accurate, clean, and efficient results. These measurements can mean the difference between quick success and machine failure—and between a polished result and a botched edge finish.
Defining These Metal Cutting Terms
Before we jump into practical advice, it’s important to understand what cutting speed and feed rate are.
Cutting Speed
Cutting speed refers to how fast the cutting edge of your tool moves across the surface of the material. You may see cutting speed measured in feet per minute (ft/min) or meters per minute (m/min). This measurement impacts heat generation, tool wear, and the risk of imperfections.
For example, a faster cutting speed might work well with softer materials but could prematurely wear your blade or create burrs on harder metals. Maintaining the correct cutting speed ensures your equipment performs optimally and delivers a smooth finish.
Feed Rate
Feed rate, on the other hand, describes the speed at which the workpiece is fed into the cutting tool. You can keep track of the feed rate in measurements of inches per minute (ipm) or millimeters per minute (mm/min). This rate determines how much material is being removed with each pass of the cutting tool.
An over-aggressive feed rate can lead to friction, vibration, and even blade failure, while too slow a rate may result in wasted time and inadequate material removal. Finding the right balance is crucial for efficiency and quality.
Getting Cutting Speed Right for Your Project
Several key factors come into play when determining the right cutting speed to use.
Consider the Hardness of Your Metal
Different metals have varying levels of hardness, which directly influences the cutting speed. A softer metal like aluminum allows for higher speeds, while harder materials like carbon steel require a slower pace to prevent overheating and blade wear.
Research the properties of the metal you’re working with, and adjust your speed accordingly.
Think About the Type of Finish You Want
Higher speeds can often result in smoother cuts, ideal for projects requiring polished finishes. However, such high speeds might compromise precision in some scenarios, especially with tougher materials.
If surface finish is a priority for your project, make incremental changes to your cutting speed, and evaluate the results. This way, you can prioritize accuracy without introducing excessive wear to your tooling.
Factor In Your Equipment

Some machines generate more vibration when handling higher speeds, impacting cut quality. Similarly, your blades may have speed limits to ensure longevity. Always consult your machine’s manual, and verify your blade’s manufacturer recommendations for speed ranges to avoid unexpected damage.
Check a Cutting Speed Chart
If you’re not sure where to start, a cutting speed chart can be a helpful guide. These charts provide standard recommendations for cutting speeds based on the material being worked on and the type of tool being used. It’s a simple yet invaluable resource for professionals and hobbyists alike, saving time and effort while delivering better results.
Document Your Settings
Once you’ve dialed in the perfect cutting speed, be sure to document your settings for future reference. This saves time when working on similar materials or projects in the future and helps maintain consistency in your work. Having a record of successful settings is particularly useful for large projects involving repeated cuts.
Key Tips for Controlling the Feed Rate
Just as cutting speed is essential for precision and efficiency, feed rate deserves equal consideration. Follow these tips to master it.
Familiarize Yourself With Your Tool First
Spend time understanding your equipment’s capabilities and limitations when it comes to feed rates. Newer tools with advanced technology may allow for higher feed rates without sacrificing quality, but older tools might require more conservative settings.
Start by running test cuts on scrap material, and listen for changes in sound or feel as the feed rate increases or decreases. This simple step can save you from mistakes when cutting your actual project material.
Start Slower
Slower feed rates are safe jumping-off points, especially if you’re new to the machine or working with a new material. A slower rate gives you greater control and allows you to observe how your material and blade are responding.
Pay attention to how smoothly the material feeds into the blade and whether any visible imperfections arise. Gradually increase the speed only when you’re confident everything is running smoothly.
Monitor for Any Issues
Even when you’ve settled on a feed rate that feels appropriate, don’t set it and forget it. Always keep an eye—or an ear—on the cutting process for signs of trouble.
Strange noises, chips that seem too large or discolored, or visible tool wear might indicate that adjustments are needed. Act quickly to prevent damage to either your machine or your material.
Keep Your Tools Clean and Sharp

Dull blades or bits increase friction, making it difficult to achieve clean cuts and forcing you to use slower feed rates. This not only impacts your efficiency but also increases the risk of damaging your material.
Make it a habit to clean your tools regularly, removing any debris, resin, or material buildup. Proper maintenance ensures your tools stay in top condition and deliver consistent results.
Sharpen blades, or replace worn-out bits as needed. A sharp tool allows for smoother feeds, better precision, and less strain on your equipment, enabling you to work at optimal feed rates without sacrificing quality.
Succeed In Your Metal Cutting Projects
Now that you understand cutting speed and feed rate for metal cutting, you can optimize your process to achieve cleaner cuts and greater efficiency.
However, achieving success in metal cutting isn’t just about technique—it also comes down to the quality of your tools. If you want to ensure your tools are up to the challenge, we recommend investing in high-quality saw blades.
At Cold Saw Shop, we specialize in steel-cutting saw blades designed for maximum performance and durability. Check out our selection, and get the best for your project.