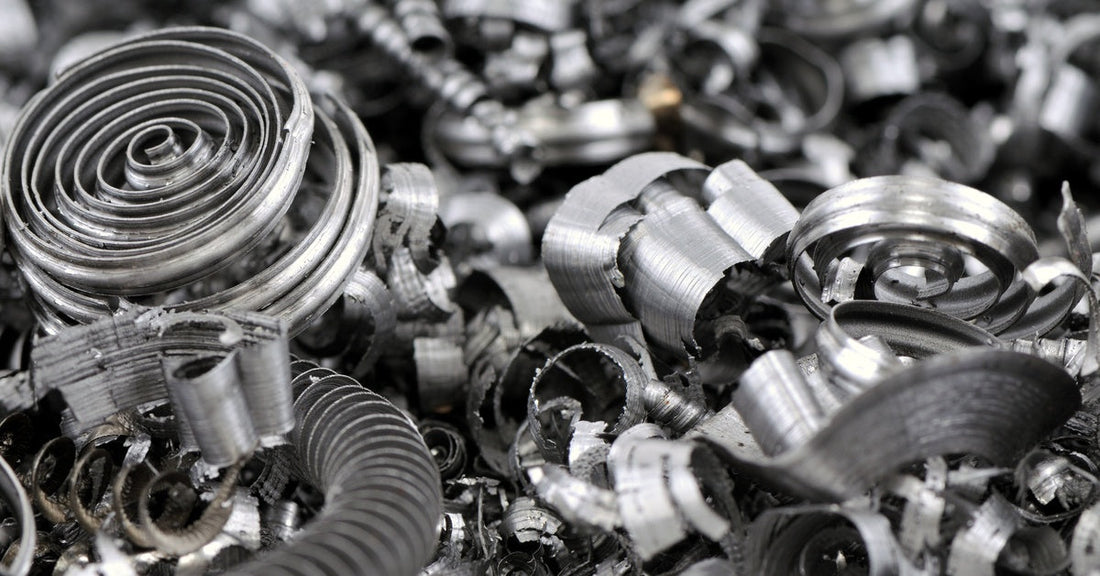
Tips for Minimizing Waste in Metal-Cutting Operations
Running an efficient metal-cutting operation demands a sound strategy. Every wasted inch of material could mean lost profits and reduced productivity. These actionable tips for minimizing waste in metal-cutting operations will help you achieve smoother workflows, lower costs, and smarter material use.
Plan Your Project Carefully
Use software tools designed for layout planning to map out pieces in a way that minimizes scrap material. For example, nesting software fits smaller shapes within larger ones like puzzle pieces.
Along with precise measurements, factor in the material’s behavior under different cutting conditions. Certain alloys, for instance, warp more easily than others, requiring adjustments to prevent costly mistakes. Proactive decisions during the design phase streamline the cutting process and lower material losses, proving that planning can save more than just time but also money!
Use the Right Equipment
When cutting metals, the tools you use define the results. Investing in top-notch equipment dramatically reduces waste and saves costs in the long run.
Quality Machinery
Precision is crucial. Every small miscalculation can result in unusable scraps from what was once a perfectly good sheet of metal. When choosing your tools, consider robustness and the ability to maintain calibration under demanding conditions.
While the price of high-end equipment may feel steep at first, it paves the way for fewer errors, less downtime, and greater overall efficiency. The advantages quickly outweigh the initial investment, particularly for shops juggling complex or high-volume projects.
Sharp Blades

For those shops working with hard materials, using a sharp cold cut saw blade produces clean, precise cuts every time. If your blades don’t deliver clean cuts consistently, it’s time to sharpen or replace them. Blade-sharpening services, such as those offered by Cold Saw Shop, extend the blade’s life and optimize its performance.
Optimize Parameters
The way you operate your cutting tools can either save on project material or send it straight to the scrap bin. Fine-tuning your cutting parameters brings efficient results and reduces waste.
Cutting Speed
While cutting at high speeds might seem like a quicker way to finish a project, it often leads to inaccuracies, tool wear, or overheating, especially when working with harder metals. Excessive speed can cause warping, uneven cuts, or damage to your tools, reducing their lifespan. Slower, measured speeds typically produce more precise and consistent results.
Different materials and projects require various speed settings, so monitor and assess the ideal cutting speed for each job. Experiment with your machinery, relying on manufacturer recommendations to maintain a balance between efficiency and accuracy.
Feed Rate
Feeding materials too quickly increases the risk of damaging your tools, producing rough cuts, and compromising the integrity of the product. Conversely, feeding materials too slowly may preserve your tools but can drastically hinder the efficiency of your workflow, delaying project timelines.
The key is to find a balance that suits the material and the type of blade or tool being used. Take the time to test and refine feed rates based on the specific properties of the material, such as its hardness or thickness, and the capabilities of your cutting equipment.
Use Efficient Cutting Techniques
Pay attention to the adjustments in positioning, pressure, and angle, as even small changes can have a big impact on the quality of your cuts. Experiment with different techniques to find the optimal settings for various materials, as the approach may vary based on thickness, composition, and even the type of cutting tool you use. Understand how each variable affects the outcome, and don’t hesitate to test new methods for improved precision.
Regular practice is key. Dedicate time to refining your skills to achieve clean, accurate cuts every time. By minimizing errors, you’ll save time and reduce wasted material, leading to greater efficiency and cost savings overall. Consistently evaluating and improving your technique will ensure that your workflow is as effective and streamlined as possible, allowing you to reduce waste over time.
Keep Up With Maintenance
Neglecting upkeep leads to dysfunctional equipment, which produces substandard cuts and errors. That’s why maintenance is another one of our top tips for minimizing waste in metal-cutting operations.
Make Repairs
Faulty machines can disrupt your workflow and create misaligned cuts, ultimately leading to higher scrap rates and wasted resources. When parts like gears break, blades become dull, or calibration systems wear out, the precision of your machinery is compromised. Addressing these issues promptly is crucial to maintaining accuracy and minimizing errors. Make it a priority to repair or replace faulty components as soon as problems arise.
Keep It Clean
Over time, dirt, debris, and residue can build up on blades and other machinery, affecting cut accuracy. Regular cleaning removes obstructions so your tools operate at their best. Additionally, establishing a cleaning routine extends the lifespan of your equipment by preventing unnecessary wear and tear caused by accumulated grime.
Repurpose Waste Where Possible
Even the most efficient metal-cutting operations will generate leftover material, but it doesn’t have to go to waste. Offcuts or scraps can often be repurposed for smaller projects or prototypes, such as creating brackets, small fixtures, or test parts for new designs, reducing material expenses.
If you can’t find a use for your scraps, consider recycling them. Many metal fabrication shops have scrapyards that will purchase your excess material, providing an additional source of income and reducing waste in the process.
Track the Results

Efficiency isn’t a one-time achievement. It’s a process. Knowing what works and what doesn’t requires mindful tracking. Analyze wastage before and after implementing adjustments, such as new tools or optimized cutting parameters. Regularly review your techniques to fix bottlenecks and refine systems.
Software tools built for tracking material use can offer valuable insights specific to your operation. Combine these insights with feedback from your cutting team to continuously optimize performance. Fine-tuning your approach consistently yields long-term benefits, ensuring success in minimizing waste across all stages of production.