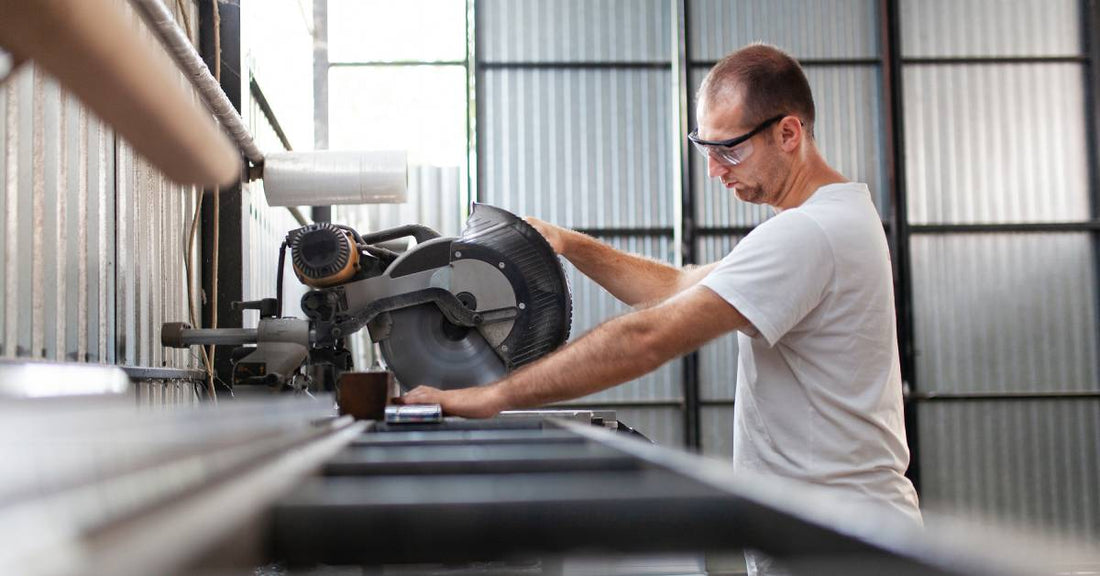
How To Improve the Efficiency of Metal Cutting
With so many projects lined up and tight deadlines looming, it’s natural to feel like you just can’t get through the work as fast as you’d like. But with some strategic adjustments, you can improve the way you cut metal. Here’s how to improve the efficiency of metal cutting without sacrificing quality.
Choose High-Quality Equipment
The foundation of efficient metal cutting starts with the right tools and machines. High-quality equipment increases the speed of project completion, remains functional after numerous uses, and cuts pieces with precision. While premium tools may require a higher upfront investment, the benefits of the machinery’s performance and longevity make it worthwhile.
Durable Design
Choose tools with sturdy, well-balanced designs that minimize vibration. A durable build can withstand wear and tear, handling rigorous use without breaking down or losing effectiveness.
High-Performance Materials
If you want your projects to benefit from clean cuts and fast workflows, choose tools made from advanced materials like carbide or compound alloys. These materials improve cutting precision, resist wear, and maintain their sharp blades for longer.
Consistent and Reliable Operation
Look for machines with minimal chatter and consistent performance. Reliable equipment delivers smoother cuts, reduces the need for rework, and saves time, ensuring better results from the first use.
Get Familiar With Your Tool
Switching to new equipment comes with a learning curve. Pay attention to tool tuning instructions and perform a few test cuts on scrap material before using the tool in a real production environment.
The more you practice, the more instinctive your movements will become. Soon, operating the new tool will feel like second nature, resulting in heightened efficiency.
Optimize Speed and Feed
Speed is the rotation of the cutting tool, while feed refers to how quickly the material moves toward it. Managing these two factors plays a huge role in how efficient you are at metal cutting.
Adjust the Tool According to the Metal
Soft metals like aluminum may allow for high speeds and feed rates, while hard materials like stainless steel work better with slow, deliberate movements. Understanding these differences can help you dial in the ideal settings for each job.
Carefully Set the Speed To Protect the Tool
Pushing your tools too hard to speed up production frequently results in overheating and premature wear. On the other hand, setting the tool to slow speeds can create inefficiencies. Monitor tool performance regularly and make incremental adjustments to find a sweet spot where speed and minimal wear align.
Strengthen Your Technique
The longer you work at metal cutting, the better your skills will become. However, this is only possible if you’re practicing with proper techniques. Ditch the bad habits and use the following best practices.
Align the Blade

Â
Proper blade alignment is crucial for achieving clean, precise cuts and avoiding unnecessary complications during your project. Before every cut, ensure the blade is perfectly aligned with the workpiece. Even small deviations can throw off your entire workflow.
Always double-check your setup, verifying that the blade is secure and in the correct position before hitting start. Spending a few extra moments on blade alignment can save you from major errors.
Use the Right Cutting Angles
Pay close attention to the cutting angles. Adjust them based on the material you’re working on. For instance, steep angles tend to work better for hard metals, while shallow angles provide smooth cuts for soft metals.
A precise angle reduces resistance during the cut, speeding up the process and preserving tool sharpness.
Maintain Your Equipment
Regular care ensures smoother operations, minimizes downtime, and keeps your tools performing at their best, saving you time and money.
Machine Calibration
Over time, even the most advanced machines can drift out of alignment, leading to inefficiencies in your operations. A machine that is slightly out of specification can result in wasted materials, flawed products, and unnecessary rework. This not only increases costs but also takes away valuable time that you could use for more productive, profitable tasks.
Periodically recalibrate your metal cutting machines. This will guarantee that your tools deliver consistent, high-quality results.
Blade Sharpening

Â
Over time, even the best blades lose their sharpness. A dull blade slows the cutting process and produces inferior results. Whether you’re working with a cold saw blade, hacksaw, or band saw, maintaining sharp blades should be a top priority.
Here at Cold Saw Shop, we offer cold saw blade sharpening services. With professional sharpening, your blades will last longer and cut faster, reducing downtime and increasing the efficiency of your work.
Keep the Tool Clean
Over time, tools and machines accumulate dust, oil, and metal shavings that negatively affect their performance. This buildup reduces efficiency and can lead to breakdowns or costly repairs.
Consider blowing away debris after every use, wiping down machines at the end of each shift, or scheduling a thorough cleaning periodically. By keeping your tools and equipment clean, you can extend their lifespan, ensure they function at their best, and ultimately save time and money in the long run.
Consider Adding Automation to Your Processes
Automation is revolutionizing metalworking processes. While it may not be suitable for every setup, automated tools can take efficiency to levels that manual operations simply can’t achieve.
Computer numerical control (CNC) machines, for example, can consistently execute complex cuts with minimal human input. Automated tools, like robotic arms, allow more flexibility when scaling production. By removing tedious, repetitive tasks from your hands, automation frees up time for projects that demand more creativity or oversight.
Measure and Adjust
Lastly, don’t assume that your metal-cutting machines are running at peak efficiency. By tracking data, you’ll gain invaluable insights into your processes. From there, identify areas for improvement and fine-tune your approach for better results.
Collect Data As You Work
Document tool performance, material types, and cutting times to identify patterns or inefficiencies. Tools like Internet of Things (IoT) sensors can provide detailed operational metrics that reveal how efficiently your setup is running.
Start Benefiting From a More Efficient Metal Cutting Process
Once you know how to improve the efficiency of metal cutting according to your setup, you’ll save valuable time, minimize cost, and deliver impeccable work to your clients. Let Cold Saw Shop be a resource of high-quality products to improve your projects. Shop our saw blades or sign up for a blade sharpening service to enhance the quality of your cuts.