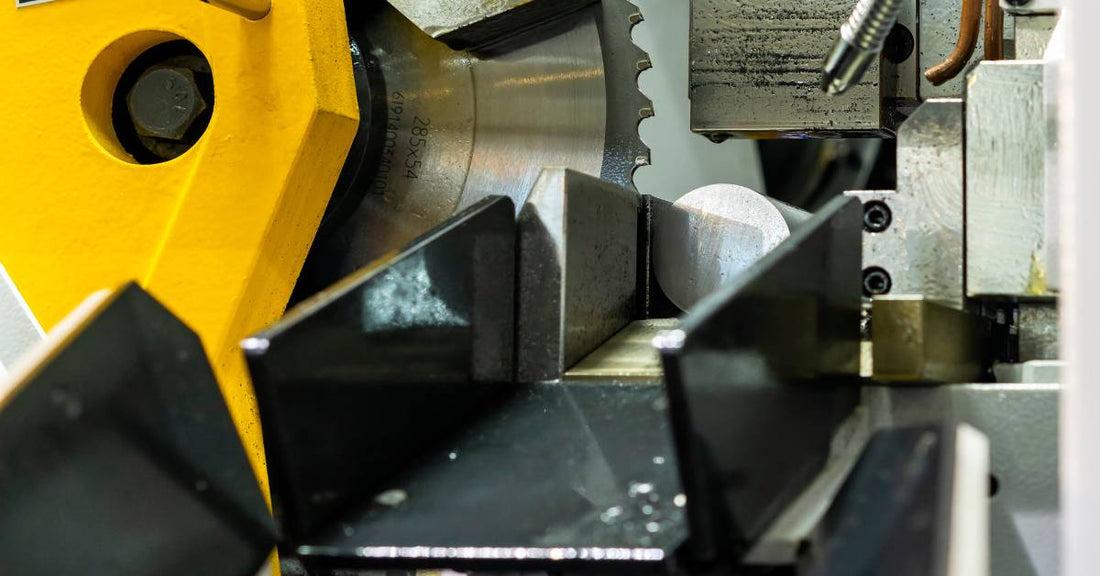
Band Saw vs. Cold Saw: What’s the Difference?
You always need the right tools when you’re dealing with cutting metal. There are a few popular options when trying to find the best tool for a specific task. But what’s the difference between band saws and cold saws? How do you know which one is the right choice? Cold Saw Shop is here to go over both pieces of equipment and discuss some of the general pros and cons to help you make an informed decision.
Understanding Band Saws
Band saws are versatile tools that are common in both metalworking and woodworking because they can make very precise cuts. A band saw consists of a continuous band of toothed metal, which rotates on two wheels to cut through the material.
Their design allows for a variety of cuts, including straight, curved, and irregular shapes, making it ideal for custom and intricate work. Key features of band saws include adjustable blade speeds, which you can tailor to the type of material you’re cutting, and varying blade widths, which impact the precision and type of cut performed.
Pros of Band Saws
Versatility
Band saws can make a variety of cuts, including straight, curved, irregular shapes, and intricate designs, making them highly versatile tools in metalworking.
Adjustable Blade Speeds
The ability to adjust blade speeds allows for optimal cutting performance across different types of materials, whether soft or hard metals.
Wide Range of Blade Widths
Different blade widths cater to various cutting needs, from narrow blades for intricate work to wider blades for straight, deep cuts.

Large Cutting Capacity
Band saws can handle a wide range of material sizes and thicknesses, making them suitable for many different projects.
Durable and Stable
Modern band saws have robust frames and durable construction to minimize vibrations and ensure stability.
Cons of Band Saws
Frequent Blade Maintenance
Band saw blades may wear out more quickly when cutting harder materials, meaning you need to replace them more frequently, especially when working with metal.
Initial Cost
High-quality band saws can be expensive, which might be a significant investment for hobbyists or small workshops.
Space Requirements
Band saws, especially larger models, require considerable workshop space. It may be harder for people to use them effectively in smaller work areas.
Noise and Dust
Operating a band saw can be noisy, and they tend to generate a lot of dust. You may need to take additional measures to control the dust and protect your hearing.
Understanding Cold Saws
Cold saws are precision tools for cutting metal with exceptional accuracy. Unlike band saws, cold saws operate with a circular saw blade made of either high-speed steel (HSS) or tungsten carbide-tipped (TCT) material. This blade typically rotates at lower speeds yet delivers highly precise cuts with minimal heat generation. The name “cold saw” comes from the fact that, during the cutting process, the blade and the material remain relatively cool, preventing thermal distortion and preserving material properties.
Another significant feature is the gearbox drive system, which provides consistent power and torque, ensuring smooth, even cuts throughout the material. Clamping systems in cold saws securely hold the material in place, reducing vibration and movement during cutting, which is crucial for achieving precise cuts. Cold saws also feature coolant systems that further help in maintaining low temperatures and extending both the blade and the machine’s life.
Pros of Cold Saws
Precision Cuts
Cold saws are very capable of delivering precise, clean, and burr-free cuts, making them ideal for applications where accuracy is important.
Low Heat Generation
Due to their low-RPM blade rotation and coolant systems, cold saws don’t generate much heat during cutting, reducing the risk of thermal distortion and preserving material properties.

Durability
The high-speed steel (HSS) or carbide-tipped blades used in cold saws are highly durable, and owners can resharpen them, which helps them have a longer lifespan than other blades.
Robust Construction
Cold saws have heavy-duty frames and robust construction, ensuring stability and minimal vibrations during the cutting process.
Efficient Clamping Systems
These saws often feature advanced clamping systems that securely hold the material in place, reducing movement and enhancing cut precision.
Adjustable Cutting Angles
The ability to perform miter cuts with high accuracy is a significant advantage, expanding the versatility of cold saws for different types of cuts.
Swarf Collection Systems
Integrated swarf collection systems manage metal shavings and debris, keeping the workspace clean and reducing maintenance time.
Cons of Cold Saws
Higher Initial Cost
Cold saws typically come with a higher initial investment compared to other types of saws, which may be a barrier for smaller workshops or hobbyists.
Lower Cutting Speed
The low-RPM operation, while advantageous for precision, results in slower cutting speeds, which makes them less ideal for high-volume production jobs.
Complex Maintenance
While owners can resharpen the blades, the process requires skill and the right equipment. This can result in increased maintenance complexity and costs.
Limited Flexibility
While cold saws are good at creating straight cuts at nearly any angle, they lack some of the versatility that helps them make intricate or more curvaceous cuts.
Space Requirements
Like band saws, cold saws often require substantial workshop space due to their size and the need for additional components like coolant systems.
Learning Curve
Operating a cold saw effectively demands practice and experience, especially in achieving precise miter cuts and maintaining the equipment.
Which Saw Is Better?
Now that you know what’s the difference between band saws and cold saws, you may wonder which one is better. Ultimately, the decision comes down to the specific requirements of your metalworking tasks. If versatility and the ability to perform a variety of cuts are your priorities, a band saw might be the better option. Alternatively, if precision and maintaining material properties are critical, investing in a cold saw could yield the best results. Assessing your project needs, budget, and available workspace will help you determine which saw aligns best with your metalworking goals.
Are you ready to elevate your metalworking projects with unmatched precision and efficiency? Cold Saw Shop offers a wide range of high-quality cold cut metal saw blade options that ensure clean, burr-free cuts every time.
Whether you’re tackling high-precision tasks or looking to maintain the integrity of your materials, our selection of durable, reliable cold saws is just what you need. Contact Cold Saw Shop today and discover how our products can transform your workshop into a cutting-edge space for precision metalworking!