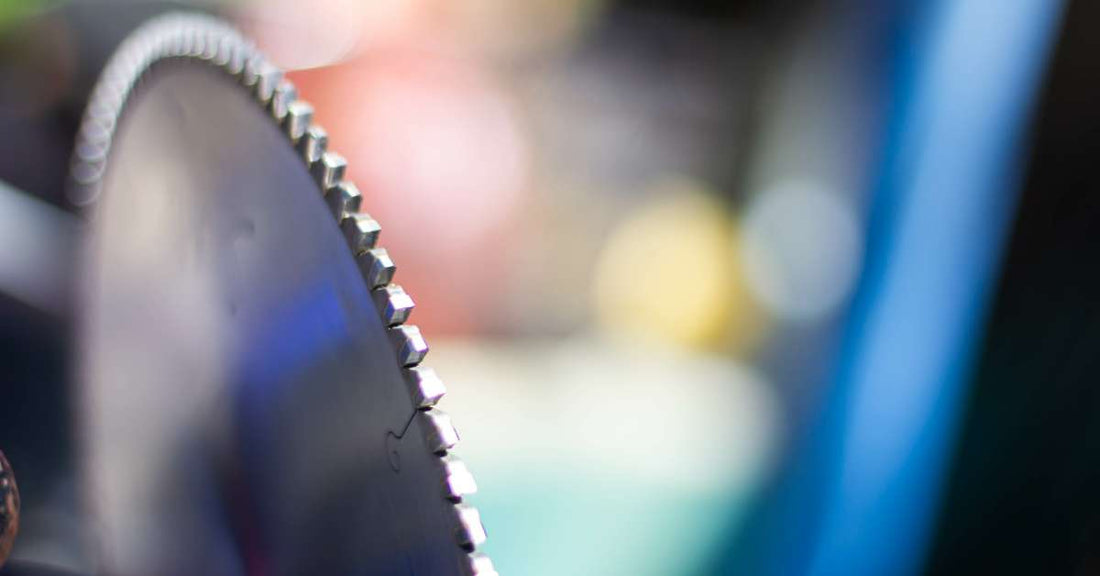
A Look at the History of Cold Saws and Carbide Sawing
There’s a great deal of history and lore when it comes to advancements in the field of metalworking tools. Among these revolutionary advancements are the cold saw and carbide sawing. Thanks to modern technology and a robust history built on improvements, we can accomplish things that seemed impossible only a few short decades ago. Today, the Cold Saw Shop is here to look at the history of cold saws and carbide sawing and see how much they’ve changed the field.
The Birth of Cold Saws
Since their earliest introduction, cold saws have been a game-changer in the metalworking field. Unlike traditional saws that generate high heat and can compromise material integrity, cold saws operate at low speeds, producing minimal heat. We first started seeing this innovation in the early 20th century when metalworkers sought more efficient ways to cut metals without distorting them.
The initial designs were rudimentary, but they laid the groundwork for the sophisticated cold saws we use today. Early cold saws were hand-operated and required considerable skill, but their ability to produce clean, precise cuts quickly made them popular.
Evolution of Cold Saw Technology
As technology advanced, so did the design and functionality of cold saws. The introduction of electric motors in the mid-20th century revolutionized cold sawing, making it faster and more efficient. These motorized saws could maintain consistent speeds, resulting in even more precise cuts.
Further development of hardened steel cold saw blades significantly improved the durability and lifespan of cold saws. By the late 20th century, cold saws were an essential tool in metalworking shops worldwide and had a distinct reputation for their precision, longevity, and general usefulness.
Introduction of Carbide Sawing
While cold saws were a significant advancement, the introduction of carbide sawing took metal cutting to a whole new level. Carbide saw blades, which use a composite material of carbon and tungsten, are incredibly hard and wear-resistant.
These blades can cut through some of the toughest metals and typically maintain their sharpness for much longer than the more common steel blades of the era. The concept of carbide sawing started picking up traction in the 1970s, driven by the need for more durable cutting tools in industrial applications.
The inherent strength of carbide meant that saw blades could maintain their cutting edge even under extreme conditions, making them ideal for high-volume production environments.

Benefits of Carbide Sawing
Carbide sawing offers numerous benefits that make it a staple part of modern metalworking. One of the most significant advantages is its ability to maintain sharpness over extended periods, reducing the need for frequent blade changes.
This longevity translates to lower operating costs and increased productivity. Carbide saw blades produce cleaner cuts with less burr formation, reducing the need for secondary finishing processes. These blades operate at higher speeds, allowing for faster cutting without compromising precision. Metalworkers appreciate the advances that came from carbide sawing since it results in more efficient, safer operations with a high-quality output.
Technological Advancements in Carbide Saw Blades
When looking at the history of cold saws and carbide sawing, there’s no denying the level of innovation that comes alongside them. Modern carbide blades feature advanced coatings that further enhance their wear resistance and cutting performance.
These coatings typically use the materials titanium or aluminum to provide additional protection against heat and corrosion. Further advancements in blade geometry optimize cutting efficiency, with specialized tooth designs making them more suitable for different types of metal. Ongoing technological improvements make carbide saw blades more versatile and effective, capable of handling a wide range of metalworking tasks with ease.
Cold Saws vs. Carbide Saws
While both cold saws and carbide saws offer advantages that benefit the craft and industry, understanding their differences can help metalworkers choose the right tool for the job. Cold saws are ideal for applications requiring precise, low-speed cuts with minimal heat generation.
They are particularly effective for cutting thin-walled tubes and profiles where maintaining material integrity is crucial. On the other hand, carbide saws excel in high-speed cutting applications, making them suitable for heavy-duty tasks involving thick, hard metals. The choice between cold saws and carbide saws ultimately depends on the specific requirements of the project, including the type of material, desired cut quality, and production volume.
Impact on the Metalworking Industry
The advent of cold saws and carbide sawing has had a profound impact on the metalworking industry. These tools have improved cutting precision and efficiency and have enabled the development of new manufacturing techniques.
The ability to produce clean, accurate cuts facilitates the use of automated cutting systems, streamlining production processes and reducing manual labor. Additionally, the durability and reliability of these tools have contributed to higher-quality end products, enhancing the overall competitiveness of metalworking businesses. The widespread adoption of cold saws and carbide sawing has transformed metalworking into a more efficient and precise industry.

Safety Considerations
Every metalworker who puts their hands on a saw should pay attention to safety, and it continues to be one of the most important aspects of metalworking. Technical advancements in cold saw cutting make the process safer and more manageable, but workers still need to take proper precautions.
This includes wearing appropriate personal protective equipment (PPE), such as gloves, safety glasses, and hearing protection. Workers should maintain and inspect saw blades and equipment to reduce the risk of accidents and ensure optimal performance. Training operators on the correct use and handling of these tools is also crucial, as improper use can lead to serious injuries.
Future Trends in Sawing Technology
The future of sawing technology holds exciting possibilities, driven by ongoing advancements in materials science and automation. One emerging trend is the development of intelligent saws that use sensors and assistive AI algorithms that can optimize cutting parameters in real time.
These smart saws can adjust blade speed, feed rate, and cutting angle based on the material being cut, resulting in even greater precision and efficiency. Innovations in blade materials and coatings continue to push the boundaries of performance and durability. The integration of digital technologies and data analytics will also play a significant role, enabling predictive maintenance and improving overall productivity.
No matter what type of metalworking project you’re working on, you can find quality cold saw blades and carbide sawing blades right here at Cold Saw Shop. Our online catalog offers a wide variety of blades in different styles, sizes, coatings, and materials that can handle the toughest metalworking tasks. Visit Cold Saw Shop today to find the perfect blade for your next project and experience unmatched cutting efficiency!