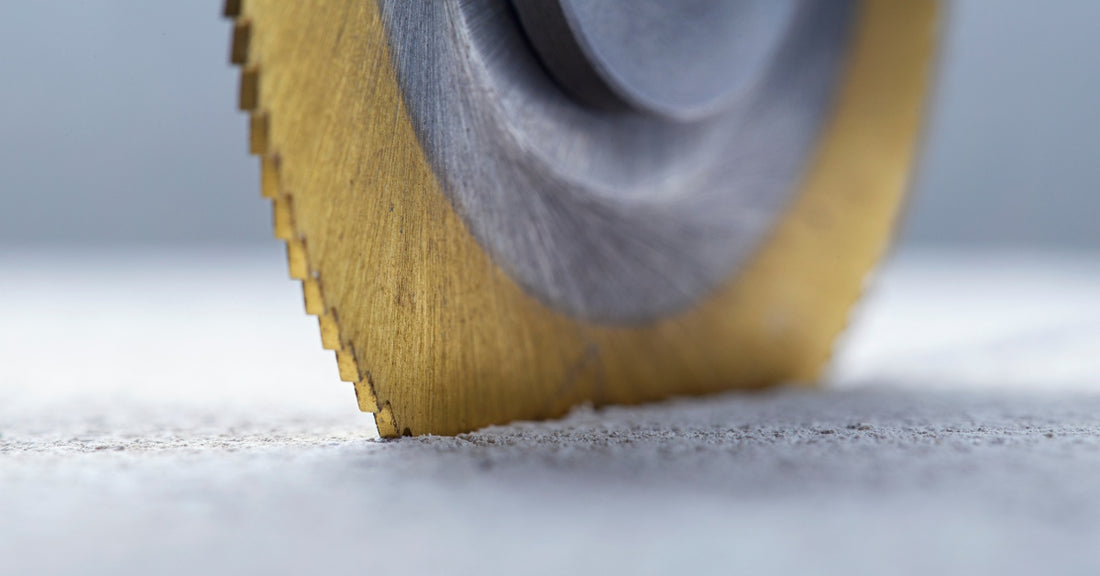
7 Different Saw Blade Coatings and Their Applications
There are many factors that go into what job a sawblade excels at. In the realm of metalworking, you may need to consider factors such as the size, shape, and physical spacing of the teeth to cut through different types of metal.
However, one of the most important factors to bear in mind is the specific coating on your saw blade, as this can make a huge difference depending on what materials you’re working with. Today, Cold Saw Shop wants to go over seven different saw blade coatings and their applications to give metalworkers an opportunity to find what coating they may need for a specific task.
Titanium Nitride (TiN) Coating
Titanium nitride (TiN) coating is one of the most widely used coatings in the metalworking industry due to its exceptional hardness and ability to significantly extend the life of saw blades. It’s easy to identify TiN coating by its distinct golden color. It provides a robust surface to enhance the performance of your blade. TiN coating increases the surface hardness, which allows the blade to cut through harder materials with greater ease and precision.
TiN coating also offers excellent resistance to wear and oxidation, which is essential in preventing the blade from dulling or deteriorating quickly. The reduced friction between the blade and the material it’s cutting also contributes to lower heat generation during operation.
Titanium Carbonitride (TiCN) Coating
Titanium carbonitride (TiCN) coating is another highly effective option for optimizing the performance of saw blades in the metalworking industry. It has a strong reputation for its hardness and toughness compared to other titanium coating options and features a gray or bluish-gray color.
The TiCN coating substantially reduces friction, which not only decreases the heat generated during cutting but also minimizes the risk of blade chipping or breakage. These features make it an excellent choice for applications involving abrasive metals and high-speed cutting operations.

Â
Diamond Coating
When you’re looking for a strong coating, you can’t get much stronger than diamond, which offers hardness and durability that you’re not going to find anywhere else. This coating boasts a naturally crystalline structure, which offers exceptional cutting and blade longevity. The primary advantage of diamond-coated saw blades is their ability to cut through extremely hard materials, such as composites, ceramics, and even cemented carbides.
The superior hardness of diamond coating enables it to maintain a sharp edge far longer than conventional coatings, resulting in fewer blade changes and reduced downtime. Additionally, diamond-coated blades exhibit remarkable resistance to wear and abrasion, which ensures high-quality cuts and prolonged operational life even under the most strenuous conditions.
Chromium Nitride (CrN) Coating
Chromium nitride (CrN) coating is another noteworthy option for enhancing the performance and durability of cold cut metal saw blades in metalworking applications. CrN coating has a silverish-gray appearance and provides several significant benefits that make it a valuable choice for a variety of cutting tasks. One of the primary advantages of CrN coating is its excellent adhesion to the blade substrate, which ensures that the coating remains intact even during intensive use.
CrN coating boasts remarkable resistance to wear and corrosion, making it especially effective in environments where blades must deal with aggressive materials and conditions. This resistance translates to longer blade life, reducing the need for frequent replacements and associated operational costs. Chromium nitride's low friction coefficient minimizes heat buildup during cutting operations, preventing thermal damage to both the blade and the material it’s cutting.
Zirconium Nitride (ZrN) Coating
Zirconium nitride (ZrN) coating is a popular option for saw blades in metalworking due to its exceptional hardness and versatility. Characterized by a unique pale gold color, ZrN coating provides several advantages that make it suitable for a broad range of applications. One of the primary benefits of ZrN coating is its excellent wear resistance, which ensures that saw blades maintain their sharpness and cutting performance over an extended period.
In addition to its outstanding durability, ZrN coating offers superior resistance to corrosion, making it one of the best options for environments where excessive moisture is a common concern. The low friction coefficient of ZrN minimizes heat generation during cutting operations, which not only preserves the structural integrity of both the blade and the material it’s cutting but also results in cleaner and more precise cuts.

Â
Chrome Coating
When looking at different saw blade coatings and their applications, you may want to consider chrome coating, sometimes known as chromium coating. This is a popular option in industrial settings and is perfect for metalworking applications.
Chrome coating has a bright, reflective finish that makes it easy to identify. The coating offers both enhanced performance and a decent blade longevity length. One of the primary benefits of chrome coating is its exceptional hardness. While it’s not as tough as diamond, it still offers a stable and reliable blade that you can get a lot of mileage out of.
In addition to its hardness, chrome coating provides excellent resistance to wear and corrosion. This resistance is particularly beneficial in environments where saw blades work with abrasive materials or corrosive substances, which can quickly degrade uncoated blades. By protecting the blade from these harsh conditions, chrome coating extends the operational lifespan of the saw blade and ensures reliable performance over time.
Teflon Coating
Teflon coating, or polytetrafluoroethylene (PTFE), is a versatile option for saw blades in the metalworking industry. Just like the Teflon you hear about in cookware, it boasts helpful nonstick properties and has a distinct chemical composition. Teflon offers several benefits that cater to specific cutting needs. One of the standout advantages of Teflon coating is its exceptional resistance to heat and friction.
Teflon's nonstick properties are particularly useful when working with materials that tend to adhere to the blade, such as certain plastics or composites. This adhesive resistance prevents material buildup on the blade, maintaining a cleaner cutting edge and ensuring more consistent performance over time.
When you’re looking for high-quality, long-lasting saw blades for metalworking applications, you can find everything you need at Cold Saw Shop. We have a wide range of blades with different coatings, sizes, and teeth layouts to help you tackle your toughest projects. To learn more about what we have to offer, browse our online catalog or contact us anytime if you have any specific questions.